Air End Rebuild - Before and After Example
Our air end rebuild shop, Simple Air End Solutions, is a full service facility equipped to handle total in-house rebuilds of stationary rotary air ends and blowers. Standard rebuilds (those not requiring machining) are common, but this example shows an "extensive" rebuild recently completed in our shop.
When we receive a unit, we take pictures and log on to our Work Sheet. Then, when disassembled, we take pictures again. This particular unit showed that the rotor had welded to the face plate (pictures taken after separation of rotor and plate).

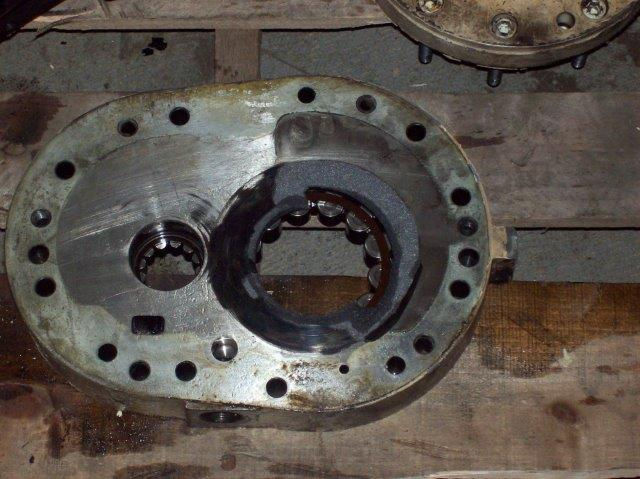
The pictures (above) show the area of the face plate where the rotor had welded onto (plate fractured after separation).
What caused the rotor to weld to the face plate?
Bearing failure will cause the rotor to drop and start running into the discharge housing. This would cause the metal to liquify on extreme high temperature and the unit will shut down . Now that the unit is off, the metal cools down and welds the two surfaces together. Remember the clearance between the face of the rotor and plate is .003 and .005 mm.
Overheating, itself, should not cause the rotor to weld itself to the discharge plate as the high temperature shut down should and will stop the machine. The main reason(s) for overheating include:
coolers have varnished or one of many other issues with oil coolers
ambient temperature is too high (100 F or more)
oil has broken down, lost viscosity
thermal valve not working properly
If the unit is run backwards it can also cause the same issue. When the air end is not running it will have the clearance (.003 to .005) between the face of the rotor and inlet plate (the end of the rotor closest to the motor); when you power up the unit, you will have 0 PSIG on both ends of the rotor. Now you start to make pressure (125 psig) on the discharge end of the rotor and discharge plate (opposite end from the motor) and the rotors start to back up. That’s why you need the clearance. If the unit runs backwards, the rotors will move in the wrong direction and hit the discharge plate. This can make metal-to-metal contact and the rotor can weld itself to the plate. And, of course, if the machine runs backwards, you have no oil pressure.
What steps are taken to remedy the issue and repair the unit?
In most cases, the rotor and faceplate can be pressed apart (as was done in this example). However, there is always a risk of cracking the housing as the weld may now be stronger than the housing. The risk is higher in some units than in other brands depending on the manufacturer. We have a large inventory of OEM cores to draw upon when this occurs, but we also have the ability to saw the rotor from the housing using a very high-tech tool for precise removal of the weld.
From the pictures above, here are the finished rotor and faceplate after machining:
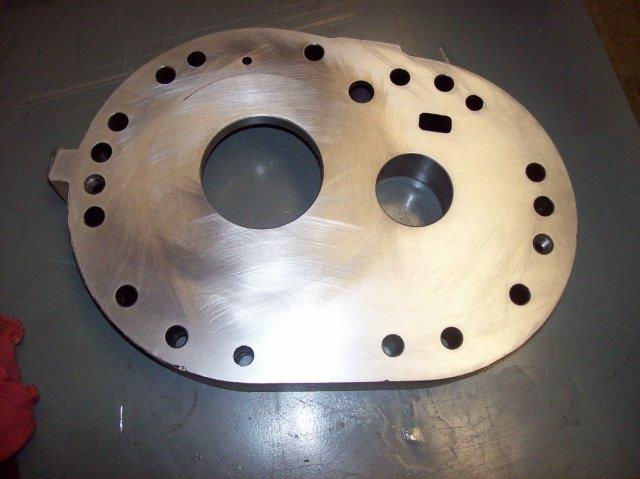

All machining and rotor balancing is done in-house. Rotor balancing (to 1/17th gram) is done on every unit. We provide a detailed step-by-step update throughout the rebuild process. Digital photos will be taken throughout the teardown, machining and rebuild process, all the way up to crating and shipping of the unit. These digital photos will be kept on file throughout the warranty period. After tearing down the air end, we will send you a firm quote and report of our findings so that you can inform your customer of the exact cost before proceeding. Once the machining is finished, the unit is cleaned, built and painted. We strap and wrap the pallet, take final pictures and ship the unit back to you.
What sets us apart from other air end rebuild shops?
Several things that we do to assure your experience with us:
Fast turnaround - 3 to 5 business days on Standard Rebuilds; 7 to 10 business days on Extensive Rebuilds
Total in-house service - all machining and rotor balancing performed in our shop
Proactive Updates - continuous communication throughout every step of the rebuild process to keep you and your customer informed of the status of the rebuild
Warranty - 12 Month Standard Warranty period; 5 Year Extended Warranty available
Quality Parts - we always use Timken or SKF bearings; never off-brand imports
Core Inventory - we have a large (300+) inventory of Cores from All Major Brands